Поверхностный монтаж печатных плат
Долгое время в электронной промышленности использовался навесной монтаж компонентов. У этого метода долгое время не было достойной альтернативы, но появились новые технологии.
Сейчас активно применяется SMT-технология — это так называемая поверхностная установка, которая имеет ряд преимуществ перед устаревшей:
- снижается себестоимость изделий,
- повышается надежность компонентов,
- размеры монтируемых элементов становятся меньше,
- проще и быстрей осуществляется монтаж,
- выполняются современные стандарты (1S0 9000),
- снижается нагрузка на производственные мощности.
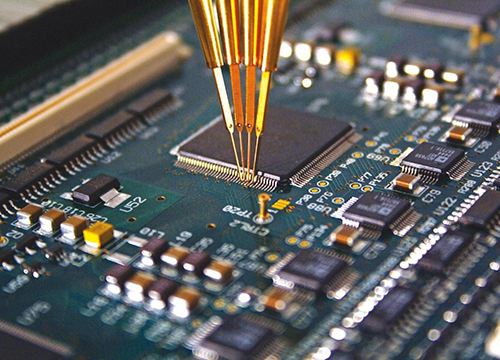
Чтобы выполнить поверхностный монтаж, необходим набор определенного оборудования. В список входят:
- аппараты для установки компонентов на печатную плату,
- устройства для нанесения и последующего оплавления паяльной пасты (припоя).
Каждый из приборов отвечает за свою функцию, а вместе они формируют законченный технологический процесс.
Нанесение пасты или припоя
Существует два основных способа нанесения паяльной пасты:
- Дозирование. Используются пневматические дозаторы, которые могут работать без использования конкретных трафаретов. То есть прибор применим к платам любых размеров и конфигураций. У метода есть существенный недостаток – скорость нанесения относительно небольшая и зависит от квалификации человека.
- Печать через трафарет (металлический или сетчатый). В этом случае применяются специальные устройства, обладающие комплексом преимуществ:
- способны обработать большой участок,
- имеют в комплекте набор дополнительных принадлежностей,
- обладают небольшой стоимостью.
Устройства трафаретной печати обеспечивают высокую производительность!
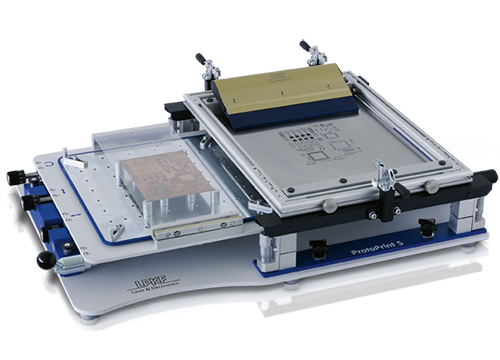
Устройства для монтажа компонентов
К числу доступных и простых в использовании приборов для поверхностного монтажа относятся ручные манипуляторы. В конструктивном плане это достаточно сложные устройства, состоящие из нескольких элементов:
- основной блок, оснащенный пантографом,
- вакуумная помпа (всегда встроена в корпус) или компрессор (располагается снаружи аппарата),
- головка, имеющая вакуумный захват,
- несколько вакуумных наконечников,
- карусельный питатель –
- отвечает за дозированную подачу элементов.
ВАЖНО: Манипуляторами управляют операторы. Именно их мастерство определяет скорость установки деталей. За 8-ми часовую смену на таком оборудовании можно смонтировать 1600–4800 элементов.
В качестве опций к манипуляторам можно заказать дополнительное оборудование:
- систему для припаивания горячим воздухом,
- альтернативные виды питателей (из пенала или из ленты),
- дозаторы пасты,
- устройства для наблюдения за процессами.
Если произвести все из указанных доработок, можно добиться производительности в 700 элементов в час!
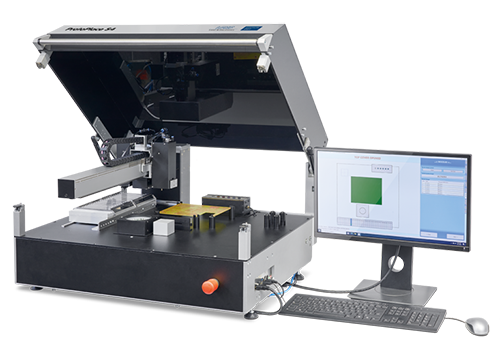
В полуавтоматических установщиках работу осуществляет человек, но все процессы контролирует компьютер. Искусственный интеллект выполняет сразу несколько полезных функций:
- показывает нужные компоненты и в каких питателях они находятся,
- указывает на место монтажа,
- фиксирует вакуумную головку в точке установки при помощи пневматических тормозов.
От человека требуется только правильно расположить деталь. И как только он делает это, головка аккуратно опускает компонент на плату.
Еще больший КПД имеют манипуляторы с системой FINE PITCH. Она обладает двумя ключевыми достоинствами:
- Позволяет точно и быстро совмещать выводные концы микросхем и места контактов на платах.
- Автоматически устанавливает элементы в нужное место.
Точность работы такова, что с помощью подобных систем можно монтировать микросхемы с шагом до 0.4 мм и элементы от 0201 (только бескорпусные).
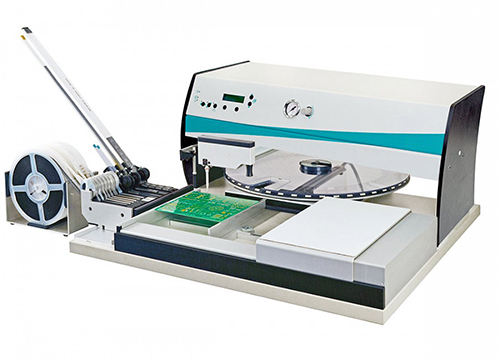
Существуют автоматические установщики, которые в данный момент являются самым совершенным оборудованием для выполнения таких задач. Устройства имеют ряд особенностей:
- максимальная производительность,
- предельная точность установки,
- быстрота перенастройки (на переход работы от одного вида плат на другой не нужно тратить много времени).
Из-за указанных характеристик стоимость автоматических манипуляторов гораздо выше, чем у ручных и полуавтоматических аналогов.
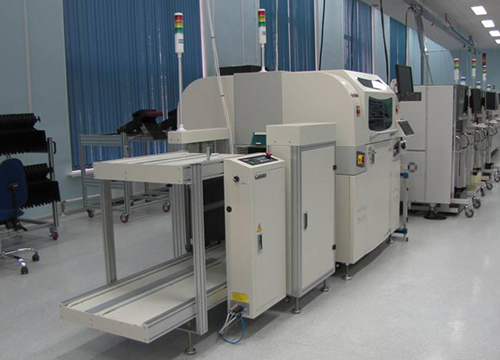
Устройства для оплавления
Завершающим этапом в монтаже компонентов на плату является оплавление паяльной пасты. Делается это при помощи «печей», которые отличаются по двум параметрам:
- метод подогрева припоя,
- количество зон разогрева.
ВАЖНО: Есть приборы с разными способами нагрева: конвекционные, инфракрасные, смешанного типа.
К простейшим относятся инфракрасные печи. Они недорогие, но используются только на платах начального уровня. Цена и ограниченная область применения обусловлена минусами этого типа нагрева. В их числе:
- температура внутри рабочих зон распределяется неравномерно,
- есть так называемый «теневой эффект», при котором высокие детали перекрывают некоторые зоны припоя,
- тепло отражается от корпусов компонентов.
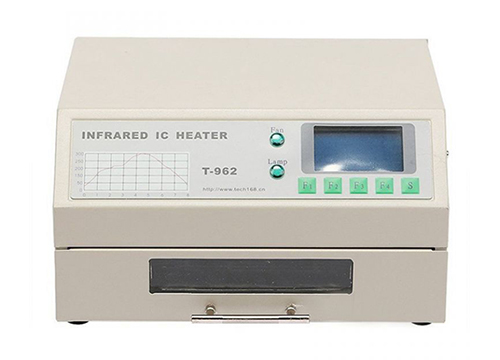
У конвекционного нагрева нет ни одного из указанных недостатков. Разогрев элементов происходит равномерно, отсутствует отражающий эффект. Такие характеристики возможны благодаря применению более совершенных технологий. Они определяют стоимость печей с конвекцией, которая зачастую очень высока.
Конвекционными устройствами начального уровня для оплавления паяльной пасты являются:
- манипуляторы с ручным или полуавтоматическим управлением,
- аппараты для трафаретной печати,
- печи оплавления.
Кроме указанного оборудования существуют более совершенные модели. Но перечисленных устройств в большинстве случаев достаточно, чтобы организовать производственный процесс или создать отдельный рабочий участок.
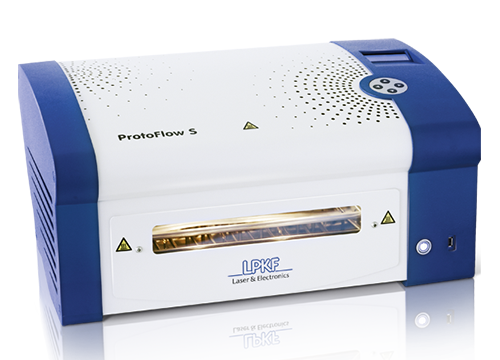
Этапы поверхностного монтажа печатных плат
Если разбирать монтаж компонентов на платы детально, то он состоит из разных технологических процессов:
- проверка поступающих плат и компонентов на наличие дефектов,
- сортировка материалов и подготовка их к монтажу,
- нанесение паяльной пасты,
- установка деталей,
- доведение клея до нужной консистенции,
- оплавка припоя,
- мытье платы,
- финальный контроль изделия,
- ремонтные работы,
- защита элементов от влаги,
- упаковка продукции.
Все помещения для подобного производства должны иметь специальное оборудование для снижения статического эффекта, улавливания дыма и вентилирования.